www.free-education.in is a platform where you can get pdf notes from 6th to 12th class notes, General Knowledge post, Engineering post, Career Guidelines , English Speaking Trick , How to crack interview and lots more. ( Isolation of Elements )
Class 12 Chemistry Chapter 6 Isolation of Elements Notes
Introduction
- Metals have lot of importance in our day to day life.
- Uses of metals:-
- The buildings around us are made up of steel, iron; wires that carry current are made up of metals.
- The bridges, tall towers are all made up of metals.
- The vessels which are made up of stainless steel; the body of ships made up of metals.
- The batteries, vehicles, engines are made up of metals.
Pure metals can be extracted from ores by some chemical reactions.
Understanding the Terms Minerals & Ores
- Mineral word is derived from the word ‘Mine’.
- The naturally occurring substances in the form of which the metals occur in the earth crust are called minerals.
- Every mineral is not suitable for the extraction of the metal.
- The mineral from which the metal is economically and conveniently extracted is called an ore.
- Thus, all ores are minerals but all minerals are not ores.
- Impurities associated with ores are called gangue or matrix.
- The extraction and isolation of metals from ores involve the following major steps:
- Concentration of the ore,
- Isolation of the metal from its concentrated ore, and
- Purification of the metal.
- The entire scientific and technological process used for isolation of the metal from its ores is known as Metallurgy.
Occurrence of Metals
- Earth crust is the source of many elements. Out of these elements, 70% are metals. Aluminium is the most abundant metal of earth crust and iron comes second.
- The percentage of different elements in earth crust is:-
- O-49%, Si-26%, Al-7.5%, Fe-4.2%, Ca-3.2%, Na-2.4%, K-2.3%, Mg-2.3%, H-l%
- Metals occur in two forms in nature:-
- In native state
- In combined state, depending upon their chemical reactivities.
Native State
Elements which have low chemical reactivity or noble metals having least electropositive character are not attacked by oxygen, moisture and CO2 of the air. These elements, therefore, occur in the Free State or in the native state, e.g., Au, Ag, Pt, S, O, N, noble gases, etc.
Combined State
Highly reactive elements such as F, CI, Na, K, etc., occur in nature combined form as their compounds such as oxides, carbonates sulphides, halides, etc.
Hydrogen is the only non-metal which exists in oxidised form only.
Extraction & Isolation of Metals
Following are the steps involved in extracting the metal, then isolating the impure metal from the ore and finally purify the metal.
- Concentration of the Ore: – The first step is to remove the impurities from the ore and it does not involve any chemical process. It is based on the difference between the physical properties of the metal and the unwanted particles.
Following are the physical processes involved:-
- Hydraulic Washing
- Magnetic separation
- Froth Flotation Method
- Leaching
- Isolation of the metal from its concentrated ore: – This process involves of getting impure metal from its concentrated ore. It is a chemical process.
Following are the processes involved:-
- Conversion of oxide (Calcination & Roasting) & Reduction to form metal.
- Electrochemical Process
- Oxidation reduction
- Purification of the metal: – It involves the purification of the metal.
Following are the processes involved:-
- Distillation
- Liquation
- Electrolysis
- Zone refining
- Vapour phase refining
- Chromatographic methods
Concentration of ores: –
- Benefaction: – Removal of the unwanted materials (e.g., sand, clays, etc.) from the ore is known as concentration, dressing or benefaction. It involves several steps and selection of these steps depends upon the differences in physical properties of the compound of the metal present and that of the gangue.
- Hydraulic Washing: – This method is based on the differences in gravities of the ore and the gangue particles. The process by which lighter earthy impurities are removed from the heavier ore particles by washing with water is called levigation. The lighter impurities are washed away. This method is commonly used for oxide ores such as haematite, tin stone and native ores of Au, Ag, etc.
- Magnetic Separation: – This method is based on differences in magnetic properties of the ore components. If either the ore or the gangue (one of these two) is capable of being attracted by a magnetic field, then such separations are carried out (e.g., in case of iron ores). The ground ore is carried on a conveyer belt which passes over a magnetic roller.
- Froth Flotation Method: – In this method is use to remove gangue from sulphide ores. In this process, a suspension of the powdered ore is made with water. This method is based on the preferential wetting of ore particles by oil and that of gangue by water .As a result the ore particles become light and rise to the top in the form of froth while the gangue particles become heavy and settle down. Thus adsorption is involved in this method.
Working of Froth Flotation Method
- It contains Collectors (e. g., pine oils, fatty acids, xanthates, etc.) which will enhance the non-wettability of the mineral particles and froth stabilisers (e. g., cresols, aniline) as a result it stabilises the froth.
- The mineral particles become wet by oils while the gangue particles by water. A rotating paddle agitates the mixture and draws air in it. As a result, froth is formed which carries the mineral particles. The froth is light and is skimmed off. It is then dried for recovery of the ore particles.
- Sometimes, it is possible to separate two sulphide ores by adjusting proportion of oil to water or by using ‘depressants’. For example, in case of an ore containing ZnS and PbS, the depressant used is NaCN. It selectively prevents ZnS from coming to the froth but allows PbS to come with the froth.
- Leaching: – Leaching is often used if the ore is soluble in some suitable solvent.
Following are the examples to explain the process of leaching.
(a) Leaching of alumina from bauxite :-
The principal ore of aluminium, bauxite, usually contains SiO2, iron oxides and titanium oxide (TiO2) as impurities.
Concentration is carried out by digesting the powdered ore with a concentrated solution of NaOH at (473 – 523) K and (35 – 36) bar pressure.
This way, Al2O3 is leached out as sodium aluminate (and SiO2 too as sodium silicate) leaving the impurities behind:
Al2O3(s) + 2NaOH (aq) + 3H2O (l) → 2Na [Al (OH) 4]( aq)
The aluminate in solution is neutralised by passing CO2 gas and hydrated Al2O3 is precipitated. At this stage, the solution is seeded with freshly prepared samples of hydrated Al2O3 which induces the precipitation
2Na [Al (OH) 4] (aq) + CO2 (g) → Al2O3.xH2O(s) + 2NaHCO3 (aq)
The sodium silicate remains in the solution and hydrated alumina is filtered, dried and heated to give back pure Al2O3:
Al2O3.xH2O(s) à Al2O3(s) + xH2O (g) (Temp at 1470K)
(b) Other examples
In the metallurgy of silver and that of gold, the respective metal is leached with a dilute solution of NaCN or KCN in the presence of air (for O2) from which the metal is obtained later by replacement:
4M(s) + 8CN– (aq) + 2H2O (aq) + O2 (g) → 4[M (CN) 2] – (aq) + 4OH– (aq)
(M= Ag or Au)
2[M (CN) 2] – (aq)] + Zn(s) à [Zn (CN) 4]2-(aq) + 2M(s)
Extraction of Crude Metals from Concentrated Ore
The concentrated ore is usually converted to oxide before reduction, as oxides are easier to reduce.
Thus, isolation of crude metal from concentrated ore involves two major steps:
- Conversion to oxide.
- Reduction of the oxides to metal.
Conversion to oxide
- Calcination: – It is the process of converting an ore into its oxides by heating it strongly, below its melting point in a limited supply of air or in absence of air.
During calcination, volatile impurities as well as organic matter and moisture are removed.
- Fe2 O3 x H2O (∆)à Fe2 O3 (s) + x H2 O (g)
- ZnCO3 (s) (∆)à ZnO(s) + CO2 (g)
- Roasting: – In roasting, the ore is heated in a regular supply of air in a furnace at a temperature below the melting point of the metal. This process is commonly used for sulphide ores and is carried out in blast furnace or reverberatory furnace. Roasting helps to remove the non-metallic impurities and moisture.
Some of the reactions involving sulphide ores are:
- 2ZnS + 3O2 → 2ZnO + 2SO2
- 2PbS + 3O2 → 2PbO + 2SO2
- 2Cu2S + 3O2 → 2Cu2O + 2SO2
If the ore contains iron, it is mixed with silica before heating.
Iron oxide ‘slags of’ as iron silicate and copper is produced in the form of copper matte which contains Cu2S and FeS.
- FeO + SiO2 → FeSiO3
- (Slag)
- Meaning of slag: – During metallurgy, ‘flux’ is added which combines with ‘gangue’ to form ‘slag’. Slag separates more easily from the ore than the gangue. This way, removal of gangue becomes easier.
Reduction of oxide to the metal
- The roasted or the calcined ore is then converted to the free metal by reduction. Reduction method depends upon the activity of metal.
- Metals which are low in the activity series (like Cu, Hg, and Au) are obtained by heating their compounds in air: metals which are in the middle of the activity “cries (like Fe. Zn, Ni, Sn) are obtained by heating their oxides with carbon while metals which are very high in the activity series (e.g., Na, K, Ca, Mg, Al) are obtained by electrolytic reduction method.
- Using the concepts of thermodynamics will help us to know the metallurgical transformations.
- Gibb’s Energy:- The change in Gibbs energy i.e. ∆G = ∆H – T∆S equation(A)
Where, ΔH is the enthalpy change and ΔS is the entropy change for the process.
- This equation can also be written as:- ΔG(-) = – RTlnK equation(1)
Where, K is the equilibrium constant of the ‘reactant – product’ system at the temperature, T. A negative ΔG implies a +ve K in equation (1).
- Following conclusions can be made:-
- When the value of ΔG is negative in equation (A), only then the reaction will proceed.
- If reactants and products of two reactions are put together in a system and the net ΔG of the two possible reactions is –ve, the overall reaction will occur.
- During reduction, the oxide of metal decomposes:
MxO(s) à xM (solid or liquid) + (1/2) O2 (g) Equation (2)
The reducing agent takes away the oxygen. Equation (2) is the reverse of the oxidation of the metal. And then, the Δf G (-) value is written in the usual way: xM(s or l) + (½) O2 (g) → MxO(s) [ΔG (-) (M, MxO)] equation (B)
- If reduction is being carried according to equation(2), the oxidation of the reducing agent(e.g. C or CO) will be:-
- C(s) + (1/2) O2(g) à CO (g) [ΔG(-) (C,CO)] equation (3)
- CO(s) + (1/2) O2(g) à CO2 (g) [ΔG(-) (C,CO)] equation(4)
- If carbon is taken, there may also be complete oxidation of the element to CO2:
- (1/2) C(s) + (1/2) O2(g) à (1/2) CO2(g) [(1/2) ΔG(C,CO2)] equation(5)
- On subtracting equation (B) from one of the three equations (3, 4 or 5).
- MxO(s) + C(s) → xM(s or l) + CO(g)
- MxO(s) + CO(g) → xM(s or l) + CO2(g)
- MxO(s) + (1/2) C(s) → xM(s or l) +( ½) CO2(g) equation(8)
- These reactions describe the actual reduction of the metal oxide, Mx
Extraction of Iron from oxide
- Oxide ores of iron, after concentration through calcination/roasting (to remove water, to decompose carbonates and to oxidise sulphides) are mixed with limestone and coke and fed into a Blast furnace from its top. In this case, the oxide is reduced to the metal.
- One of the main reduction steps in this process is:
- FeO(s) + C(s) → Fe(s/l) + CO (g)
- Consider the above reaction as 2 simpler reactions, in One reduction of FeO takes place and in another C is being oxidised to CO:
- FeO(s) → Fe(s) +( ½) O2(g) [ΔG(FeO, Fe)] equation (C)
- C(s) + (1/2) O2 (g) → CO (g) [ΔG (C, CO)]
- When both the reactions take place to yield the equation (8),
The net Gibbs energy change becomes:
ΔG (C, CO) + ΔG (FeO, Fe) = ΔrG equation (9)
- The resultant reaction will take place if RHS of the equation (9) is negative.
- In ΔG (-) vs T plot representing reaction by equation (C), the plot goes upward and that representing the change C→CO (C, CO) goes downward.
- At temperatures above 1073K (approx.),
- The (C, CO) line comes below the Fe, FeO line [ΔG (C, CO) < ΔG (Fe, FeO)].
- So in this range, coke will be reducing the FeO and will itself be oxidised to CO.
- In a similar way the reduction of Fe3O4 and Fe2O3 at relatively lower temperatures by CO can be explained on the basis of lower lying points of intersection of their curves with the CO, CO2
(Graph 1) Gibbs energy (ΔGV) vs T plots (schematic) for formation of some oxides (Ellingham diagram)
Blast Furnace
- In the Blast furnace, reduction of iron oxides takes place in different temperature ranges.
- Hot air is blown from the bottom of the furnace and coke is burnt to give temperature upto about 2200K in the lower portion itself.
- The burning of coke therefore supplies most of the heat required in the process. The CO and heat moves to upper part of the furnace.
- In upper part, the temperature is lower and the iron oxides (Fe2O3 and Fe3O4) coming from the top are reduced in steps to FeO.
- Thus, the reduction reactions taking place in the lower temperature range and in the higher temperature range, depend on the points of corresponding intersections in the ΔrG(-) vs T plots.
- Following are the reactions which are taking place:-
- At 500 – 800 K (lower temperature range in the blast furnace)–
- 3Fe2O3 + CO à 2 Fe3O4
- Fe3O4 + 4 CO à 3Fe + 4CO2
- Fe2O3 + CO à 2 FeO + CO2
- At 500 – 800 K (lower temperature range in the blast furnace)–
- At 900 – 1500 K (higher temperature range in the blast furnace):
- C + CO2 à 2 CO
- FeO + CO à Fe + CO2
Products formed in Blast Furnace
- Limestone is also decomposed to CaO which removes silicate impurity of the ore as slag. The slag is in molten state and separates out from iron.
- The iron obtained from Blast furnace contains about 4% carbon and some other impurities. This iron is known as pig iron.
- Cast iron is different from pig iron and is made by melting pig iron with scrap iron and coke using hot air blast. It has slightly lower carbon content (about 3%) and is extremely hard and brittle.
- Wrought iron or malleable iron is the purest form of commercial iron and is prepared from cast iron by oxidising impurities in a reverberatory furnace lined with haematite.
- This haematite oxidises carbon to carbon monoxide:
- Fe2O3 + 3 C → 2 Fe + 3 CO
- Limestone is added as a flux and sulphur, silicon and phosphorus are oxidised and passed into the slag. The metal is removed and freed from the slag by passing through rollers.
Extraction of copper from cuprous oxide [copper [I] oxide]
- Considering the Graph (1) the Cu2O line is at the top.
- So to reduce oxide ores of copper directly to the metal by heating with coke (both the lines of C, CO and C, CO2 are at much lower positions in the graph particularly after 500 – 600K).
- Most of the ores are sulphide and some may also contain iron. The sulphide ores
- are roasted/smelted to give oxides:
- 2Cu2S + 3O2 → 2Cu2O + 2SO2
- The oxide can then be easily reduced to metallic copper using coke:
- Cu2O + C → 2 Cu + CO
- In actual process, the ore is heated in a reverberatory furnace after mixing with silica. In the furnace, iron oxide ‘slags of’ as iron silicate and copper is produced in the form of copper matte. This contains Cu2S and FeS.
- FeO + SiO2 → FeSiO3 (Slag)
- Copper matte is then charged into silica lined convertor.
- Some silica is also added and hot air blast is blown to convert the remaining
- FeS2, FeO and Cu2S/Cu2O to the metallic copper.
- Following reactions take place:
- 2FeS + 3O2 → 2FeO + 2SO2
- FeO + SiO2 → FeSiO3 (6.38)
- 2Cu2S + 3O2 → 2Cu2O + 2SO2
- 2Cu2O + Cu2S → 6Cu + SO2
- The solidified copper obtained has blistered appearance due to the evolution of SO2 and so it is called blister copper.
- Following reactions take place:
- FeS2, FeO and Cu2S/Cu2O to the metallic copper.
Extraction of Zinc from Zinc Oxide
- The reduction of zinc oxide is done using coke. The temperature in this case is higher than that in case of copper.
- For the purpose of heating, the oxide is made into brickettes with coke and clay.
- ZnO + C àZn + CO (where coke is the catalyst, and temperature is 673 K)
- The metal is distilled off and collected by rapid chilling.
Electrochemical Principles of Metallurgy
- In the reduction of a molten metal salt, electrolysis is done.
- Consider the equation:-
- ΔG(0) = – nE(-)F equation (1)
- n= number of electrons and E(-) = electrode potential of redox couple formed in the system.
- More reactive metals have large negative values of the electrode potential.
- This implies their reduction is very difficult.
- If the difference of two E(-) values corresponds to a positive E(-) and consequently negative ΔG(0) in equation (1) .
- As a result then the less reactive metal will come out of the solution and the more reactive metal will go to the solution.
- For example:- Cu2+ (aq) + Fe(s) → Cu(s) + Fe2+ (aq)
- In simple electrolysis, the Mn+ ions are discharged at negative electrodes (cathodes) and deposited there. Sometimes a flux is added for making the molten mass more conducting.
Aluminium
- In the metallurgy of aluminium, purified Al2O3 is mixed with Na3AlF6 or CaF2 which lowers the melting point of the mix and brings conductivity.
- The fused matrix is electrolysed.
- Steel cathode and graphite anode are used. The graphite anode is useful here for reduction to the metal.
- The overall reaction may be taken as:
- 2Al2O3 + 3C → 4Al + 3CO2
- This process of electrolysis is widely known as Hall-Heroult process.
- The electrolysis of the molten mass is carried out in an electrolytic cell using carbon electrodes. The oxygen liberated at anode reacts with the carbon of anode producing CO and CO2.
- This way for each kg of aluminium produced, about 0.5 kg of carbon anode is burnt away.
- The electrolytic reactions are:
- Cathode: Al3+ (melt) + 3e– → Al(l)
- Anode: C(s) + O2– (melt) → CO(g) + 2e–
- C(s) + 2O2– (melt) → CO2 (g) + 4e–
Refining
- A metal extracted by any method is usually contaminated with some impurity.
- For obtaining metals of high purity, several techniques are used depending upon the differences in properties of the metal and the impurity.
- Following are the methods used to refine the metals:-
- Distillation
- Liquation
- Electrolysis
- Zone refining
- Vapour phase refining
- Chromatographic methods
Distillation
- This is very useful for low boiling metals like zinc and mercury. The impure metal is evaporated to obtain the pure metal as distillate.
(b) Liquation
- In this method a low melting metal like tin can be made to flow on a sloping surface. In this way it is separated from higher melting impurities.
(c) Electrolytic Refining
- In this method the impure metal is made to act as anode. A strip of the same metal in pure form is used as cathode.
- They are put in a suitable electrolytic bath containing soluble salt of the same metal.
- The more basic metal remains in the solution and the less basic ones go to the anode mud.
- The reactions are:
- Anode: M → Mn+ + ne–
- Cathode: Mn+ + ne– → M
- This method is used to refine Copper, Zinc etc.
- In case of copper refining-
- Anodes are of impure copper and pure copper strips are taken as cathode.
- The electrolyte is acidified solution of copper sulphate and the net result of electrolysis is the transfer of copper in pure form from the anode to the cathode:
- Anode: Cu → Cu2+ + 2 e–
- Cathode: Cu2+ + 2e– → Cu
- Impurities from the blister copper deposit as anode mud which contains antimony, selenium, tellurium, silver, gold and platinum; recovery of these elements may meet the cost of refining.
(d) Zone refining
- This method is based on the principle that the impurities are more soluble in the molten form as compared to the solid state of the metal.
- A circular mobile heater is fixed at one end of a rod of the impure metal.
- The molten zone moves along with the heater which is moved forward. As the heater moves forward, the pure metal crystallises out of the melt and the impurities pass on into the adjacent molten zone.
- The process is repeated several times and the heater is moved in the same direction. At one end, impurities get concentrated.
- This end is cut off. This method is very useful for producing semiconductor and other metals of very high purity, e.g., germanium, silicon, boron, gallium and indium.
- Vapour Phase Refining
- The metal is converted into its volatile compound and collected elsewhere. It is then decomposed to give pure metal.
- There are 2 requirements for this method:-
- The metal should form a volatile compound with an available reagent,
- The volatile compound should be easily decomposable, so that the recovery is easy.
- For example: – Mond Process for Refining Nickel and van Arkel Method for Refining Zirconium or Titanium.
- Chromatographic method
- The principle of this method is that different components of a mixture are differently adsorbed on an adsorbent. The mixture is put in a liquid or gaseous medium which is moved through the adsorbent.
- Different components are adsorbed at different levels on the column.
- The adsorbed components are removed or eluted by using suitable solvents (eluant).
- Depending upon the physical state of the moving medium and the adsorbent material and also on the process of passage of the moving medium, the chromatographic method is given the name.
- The Al2O3 is prepared in a glass tube and the moving medium containing a solution of the components is in liquid form. This is an example of column chromatography.
- There are several chromatographic techniques such as paper chromatography, column chromatography, gas chromatography, etc.
Diagram showing column chromatography
Uses of Aluminium, Copper, Zinc & Iron
Aluminium
- Aluminium foils are used as wrappers for chocolates.
- The fine dust of the metal is used in paints and lacquers.
- Aluminium, being highly reactive, is also used in the extraction of chromium and manganese from their oxides. Wires of aluminium are used as electricity conductors.
- Alloys containing aluminium, being light, are very useful.
Copper
- Copper is used for making wires used in electrical industry and for water and steam pipes.
- It is also used in several alloys that are rather tougher than the metal itself, e.g., brass (with zinc), bronze (with tin) and coinage alloy (with nickel).
Zinc
- Zinc is used for galvanising iron. It is also used in large quantities in batteries, as a constituent of many alloys, e.g., brass, (Cu 60%, Zn 40%) and German silver (Cu 25-30%, Zn 25-30%, Ni 40–50%).
- Zinc dust is used as a reducing agent in the manufacture of dye-stuffs, paints, etc.
Iron
- Cast iron, which is the most important form of iron, is used for casting stoves, railway sleepers, gutter pipes, toys, etc. It is used in the manufacture of wrought iron and steel.
- Wrought iron is used in making anchors, wires, bolts, chains and agricultural implements.
- Steel finds a number of uses. Alloy steel is obtained when other metals are added to it.
- Nickel steel is used for making cables, automobiles and aeroplane parts, pendulum, measuring tapes, chrome steel for cutting tools and crushing machines, and stainless steel for cycles, automobiles, utensils, pens, etc.
CBSE Class 12 Chemistry Important Questions
Chapter 6 – General Principles and Processes of Isolation of Elements
1 Mark Questions
1. What is pig iron?
Ans. The iron which is obtained from blast furnace and contains about 4% carbon and many other impurities in smaller amounts like S, P, Si, Mn etc, is called pig iron.
2. What is cast iron?
Ans. Iron obtained by melting pig iron with scrap iron and coke using hot air blast is cast iron.
3. What is wrought iron?
Ans. Wrought iron and malleable iron is the purest form of commercial iron which is prepared from cast iron by oxidizing impurities in a reverberatory furnace lined with heamatite.
4. What is added as flux in extraction of iron?
Ans. Limestone is used as flux in extraction of iron.
5. What is Blister copper?
Ans. The solidified copper obtained after extraction has blistered appearance due to evolution of is called blister copper.
6. Write the equation for reduction of zinc oxide?
Ans. The reduction of zinc-oxide is done using coke.
7. Why is cryolite used during extraction of Aluminum?
Ans. Cryolite is used to lower the melting point of alumina and increase conductivity.
8. How is copper extracted from low grade ores?
Ans. Copper is extracted by hydrometallurgy from low grade ores. It is leached out using acid or bacteria.
9. State one limitation of Ellingham diagrams.
Ans. Ellingham diagrams only tell us about the feasibility of a reaction. They do not tell anything about the reaction kinetics.
10. Give an example of extraction based on oxidation reduction.
Ans. An example based on extraction by oxidation is extraction of chlorine from brine.
11. Which method is used for refining of silicon or gallium?
Ans. The refining of Silicon or gallium is done by Zone refining.
12. What is the principle behind zone refining?
Ans. The principle of zone refining is that impurities are more soluble in the melt then in the solid state of the metal.
13. Predict conditions under which Al might be expected to reduce MgO.
Ans. Above , the standard Gibbs free energy of formation of from Al is less than that of MgO from Mg. Therefore, above , Al can reduce MgO.
14. What is the role of cryolite in the metallurgy of aluminium?
Ans. Cryolite (Na3AlF6) has two roles in the metallurgy of aluminium:
1. To decrease the melting point of the mixture from 2323 K to 1140 K.
2. To increase the electrical conductivity of .
15. Why is zinc not extracted from zinc oxide through reduction using CO?
Ans. The standard Gibbs free energy of formation of ZnO from Zn is lower than that of from CO. Therefore, CO cannot reduce ZnO to Zn. Hence, Zn is not extracted from ZnO through reduction using CO.
2 Marks Questions
1. Sulphide and carbonate ores are converted to oxide before reduction. Why?
Ans. Since the reduction of oxide ores involves a decrease in Gibb’s free energy making G value more negative, it is easier to reduce oxides therefore suphide and carbonate ores are converted to oxides before reduction.
2. What is calcinations and roasting? Give one example of each?
Ans. Calcination:- It is the process of heating carbonate ore in the absence of air when volatile matter escape leaving behind metal oxide . e.g.
Roasting :- Here ore is heated in a regular supply of air at a temperature below the melting point of metal e.g.
3. What is slag? Give an example.
Ans. Slag is the substance obtained after flux reacts with impurity.
Flux + Impurity Slag.
For example silica is added as flux to remove iron oxide during extraction of copper as ferrous silicate.
Impurity flux
4. How does a reducing agent helps in reduction?
Ans. During the reduction of the metal oxide, the reducing agent combines with oxygen of metal oxide and gets itself oxidized.
Here carbon is reducing agent.
5. Write the relationship between Gibbs free energy, enthalpy change and change in entropy?
Ans. When S is entropy change, H is enthalpy change , than at temperature T, the change in Gibbs free energy is given by
G = H – TS.
6. What is the condition for a reduction reaction to occur in terms of free energy change? How can it be achieved?
Ans. When the value of G is negative, the reduction reaction is said to be spontaneous
1) If S is positive, on increasing the temperature, the value of TS would increase & G will become negative.
2) For a process which is otherwise having G positive & is non- spontaneous, it can be coupled with a reaction having highly negative G value so that the overall G is negative and the process can take place.
7. What are Ellingham diagrams?
Ans. Ellingham diagrams are graphical representation of variation of G vs T for the formation of oxides of elements i.e., for the reaction
8. Give the requirements for vapour phase refining?
Ans. The two requirements of vapour phase refining are:-
1) The metal should form a volatile compound with an available reagent,
2) The volatile compound should be easily decomposable so that recovery is easy.
9. What is the basis of reduction of a molten metal salt? Explain
Ans. In the reduction of molten metal salt, electrolysis is done which is based on electrochemical principles following equation
Here n is the number of electrons and E0 is the electrode potential of redox couple. More reactive metals have large negative values of the electrode potential and are difficult to reduce.
10. Which of the ores mentioned in Table 6.1 can be concentrated by magnetic separation method?
Ans. If the ore or the gangue can be attracted by the magnetic field, then the ore can be concentrated by the process of magnetic separation. Among the ores mentioned in table 6.1, the ores of iron such as haematite , magnetite , siderite and iron pyrites can be separated by the process of magnetic separation.
11. The reaction, is thermodynamically feasible as is apparent from the Gibbs energy value. Why does it not take place at room temperature?
Ans. The change in Gibbs energy is related to the equilibrium constant, K as
At room temperature, all reactants and products of the given reaction are in the solid state. As a result, equilibrium does not exist between the reactants and the products. Hence, the reaction does not take place at room temperature. However, at a higher temperature, chromium melts and the reaction takes place.
We also know that according to the equation
Increasing the temperature increases the value of making the value of more and more negative. Therefore, the reaction becomes more and more feasible as the temperature is increased.
12. Is it true that under conditions, Mg can reduce and Si can reduce MgO? What are those conditions
Ans.
The temperature range in which is lesser than , Mg can reduce to Si.
On the other hand, the temperature range in which is less than , Si can reduce MgO to Mg.
The temperature at which curves of these two substances intersect is 1966 K. Thus, at temperature less than 1966 K, Mg can reduce and above 1966 K, Si can reduce MgO.
13. Copper can be extracted by hydrometallurgy but not zinc. Explain.
Ans. The reduction potentials of zinc and iron are lower than that of copper. In hydrometallurgy, zinc and iron can be used to displace copper from their solution.
But to displace zinc, more reactive metals i.e., metals having lower reduction potentials than zinc such as Mg, Ca, K, etc. are required. But all these metals react with water with the evolution of gas.
As a result, these metals cannot be used in hydrometallurgy to extract zinc.
Hence, copper can be extracted by hydrometallurgy but not zinc.
14. Out of C and CO, which is a better reducing agent at 673 K?
Ans. At 673 K, the value of is less than that of. Therefore, CO can be oxidised more easily to than C to CO. Hence, CO is a better reducing agent than C at 673 K.
15. Name the common elements present in the anode mud in electrolytic refining of copper. Why are they so present?
Ans. In electrolytic refining of copper, the common elements present in anode mud are selenium, tellurium, silver, gold, platinum, and antimony.
These elements are very less reactive and are not affected during the purification process. Hence, they settle down below the anode as anode mud.
16. What is meant by the term “chromatography”?
Ans. Chromatography is a collective term used for a family of laboratory techniques for the separation of mixtures. The term is derived from Greek words ‘chroma’ meaning ‘colour’ and ‘graphein’ meaning ‘to write’. Chromatographic techniques are based on the principle that different components are absorbed differently on an absorbent. There are several chromatographic techniques such as paper chromatography, column chromatography, gas chromatography, etc.
17. What criterion is followed for the selection of the stationary phase in chromatography?
Ans. The stationary phase is selected in such a way that the components of the sample have different solubility’s in the phase. Hence, different components have different rates of movement through the stationary phase and as a result, can be separated from each other.
18. Describe a method for refining nickel.
Ans. Nickel is refined by Mond’s process. In this process, nickel is heated in the presence of carbon monoxide to form nickel tetracarbonyl, which is a volatile complex.
Then, the obtained nickel tetracarbonyl is decomposed by subjecting it to a higher temperature (450 – 470 K) to obtain pure nickel metal.
19. How is ‘cast iron’ different from ‘pig iron”?
Ans. The iron obtained from blast furnaces is known as pig iron. It contains around 4% carbon and many impurities such as S, P, Si, Mn in smaller amounts.
Cast iron is obtained by melting pig iron and coke using a hot air blast. It contains a lower amount of carbon (3%) than pig iron. Unlike pig iron, cast iron is extremely hard and brittle.
20. Differentiate between “minerals” and “ores”.
Ans. Minerals are naturally occurring chemical substances containing metals. They are found in the Earth’s crust and are obtained by mining.
Ores are rocks and minerals viable to be used as a source of metal.
For example, there are many minerals containing zinc, but zinc cannot be extracted profitably (conveniently and economically) from all these minerals.
Zinc can be obtained from zinc blende (ZnS), calamine , Zincite (ZnO) etc.
Thus, these minerals are called ores of zinc.
21. How is leaching carried out in case of low grade copper ores?
Ans. In case of low grade copper ores, leaching is carried out using acid or bacteria in the presence of air. In this process, copper goes into the solution as ions.
The resulting solution is treated with scrap iron or to get metallic copper.
3 Marks Questions
1. How are gold and silver extracted?
Ans. Gold and silver are extracted by leaching the metal with CN–. The metal is later recovered by displacement method in which zinc acts as reducing agent.
2. Give two examples of metal refined by
a) Distillation
b) Liquation
c) Electrolytic refining
Ans. a) Distillation – Zinc and Mercury
b) Liquation – Tin and Antimony
c) Electrolytic refining – Copper and Zinc
3. Explain electrolytic refining of copper.
Ans. Electrolytic refining of copper-
In this method impure copper acts as anode and a strip of the same metal in the pure form is used as cathode. The electrolyte is acidified solution of copper sulphate. The net result is the transfer of copper in pure form from the anode to cathode.
Impurities from the blister copper like antimony, selenium, tellurium, silver, gold and platinum deposit as anode mud.
4. Write a short note on Mond’s process.
Ans. Mond’s Process- In this process, nickel is heated in a stream of carbon monoxide to give a volatile complex, nickel tetra carbonyl.
The carbonyl is heated to higher temperature
5. Which method is used for refining of zirconium? Explain.
Ans. Zirconium and Titanium are refined by van Ankle process, Here the crude metal is heated in an evacuated vessel with iodine.
The metal iodide is decomposed on a tungsten filament, electrically heated to about 1800K and pure metal is deposited on the filament.
6. What is the principle behind chromatography? Name some types of chromatographic techniques.
Ans. The principle behind chromatography is that different components of a mixture are differently adsorbed on an adsorbent. Some of the chromatographic techniques are paper chromatography, column chromatography, gas chromatography etc.
7. Explain the extraction of copper?
Ans. The sulphide ores of copper are roasted to give oxides:
The oxide can then be easily reduced to metallic copper using coke.
The impurities like iron oxide are removed as slag by reacting with, added as flux.
8. What is the role of depressant in froth floatation process?
Ans. In the froth floatation process, the role of the depressants is to separate two sulphide ores by selectively preventing one ore from forming froth. For example, to separate two sulphide ores (ZnS and Pbs), NaCN is used as a depressant which selectively allows PbS to come with froth, but prevents ZnS from coming to froth. This happens because NaCN reacts with ZnS to form .
9. Why is the extraction of copper from pyrites more difficult than that from its oxide ore through reduction?
Ans. The Gibbs free energy of formation of is less than that of and. Therefore, and C cannot reduce to Cu.
On the other hand, the Gibbs free energy of formation of is greater than that of CO. Hence, C can reduce to Cu.
Hence, the extraction of copper from its pyrite ore is difficult than from its oxide ore through reduction.
10. State the role of silica in the metallurgy of copper.
Ans. During the roasting of pyrite ore, a mixture of FeO and is obtained.
The role of silica in the metallurgy of copper is to remove the iron oxide obtained during the process of roasting as ‘slag’. If the sulphide ore of copper contains iron, then silica is added as flux before roasting. Then, FeO combines with silica to form iron silicate, (slag).
11. Why copper matte is put in silica lined converter?
Ans. Coppermatte contains and FeS. Copper matte is put in a silica-lined converter to remove the remaining FeO and FeS present in the matte as slag . Also, some silica is added to the silica-lined converter. Then, a hot air blast is blown. As a result, the remaining FeS and FeOare converted to iron silicate and is converted into metallic copper.
12. The value of for formation of is and that of is . Is the reduction of possible with Al?
Ans. The value of for the formation of from Cr () is higher than that of Al2O3 from Al (). Therefore, Al can reduce to Cr. Hence, the reduction of with Al is possible.
Alternatively,
Subtracting equation (ii) from (i), we have
As for the reduction reaction of by Al is negative, this reaction is possible.
13. Out of C and CO, which is a better reducing agent for ZnO?
Ans.
Reduction of ZnO to Zn is usually carried out at 1673 K. From the above figure, it can be observed that above 1073 K, the Gibbs free energy of formation of CO from C and above 1273 K, the Gibbs free energy of formation of from C is lesser than the Gibbs free energy of formation of ZnO. Therefore, C can easily reduce ZnO to Zn.
On the other hand, the Gibbs free energy of formation of from CO is always higher than the Gibbs free energy of formation of ZnO. Therefore, CO cannot reduce ZnO. Hence, C is a better reducing agent than CO for reducing ZnO.
5 Marks Questions
1. What is the significance of leaching in the extraction of aluminium?
Ans. In the extraction of aluminium, the significance of leaching is to concentrate pure alumina from bauxite ore.
Bauxite usually contains silica, iron oxide, and titanium oxide as impurities. In the process of leaching, alumina is concentrated by digesting the powdered ore with a concentrated solution of NaOH at 473-523 K and 35-36 bar. Under these conditions, alumina dissolves as sodium meta-aluminate and silica dissolves as sodium silicate leaving the impurities behind.
Alumina
The impurities are then filtered and the solution is neutralized by passing gas. In this process, hydrated gets precipitated and sodium silicate remains in the solution. Precipitation is induced by seeding the solution with freshly prepared samples of hydrated .
Hydrated alumina thus obtained is filtered, dried, and heated to give back pure alumina .
2. Explain: (i) Zone refining (ii) Column chromatography.
Ans. (i) Zone refining:
This method is based on the principle that impurities are more soluble in the molten state of metal (the melt) than in the solid state. In the process of zone refining, a circular mobile heater is fixed at one end of a rod of impure metal. As the heater moves, the molten zone of the rod also moves with it. As a result, pure metal crystallizes out of the melt and the impurities pass onto the adjacent molten zone. This process is repeated several times, which leads to the segregation of impurities at one end of the rod. Then, the end with the impurities is cut off. Silicon, boron, gallium, indium etc. can be purified by this process.
(ii) Column chromatography:
Column chromatography is a technique used to separate different components of a mixture. It is a very useful technique used for the purification of elements available in minute quantities. It is also used to remove the impurities that are not very different in chemical properties from the element to be purified. Chromatography is based on the principle that different components of a mixture are differently adsorbed on an adsorbent. In chromatography, there are two phases: mobile phase and stationary phase. The stationary phase is immobile and immiscible. column is usually used as the stationary phase in column chromatography. The mobile phase may be a gas, liquid, or supercritical fluid in which the sample extract is dissolved. Then, the mobile phase is forced to move through the stationary phase. The component that is more strongly adsorbed on the column takes a longer time to travel through it than the component that is weakly adsorbed. The adsorbed components are then removed (eluted) using a suitable solvent (eluant).
3. Write down the reactions taking place in different zones in the blast furnace during the extraction of iron.
Ans.
During the extraction of iron, the reduction of iron oxides takes place in the blast furnace. In this process, hot air is blown from the bottom of the furnace and coke is burnt to raise the temperature up to 2200 K in the lower portion itself. The temperature is lower in the upper part. Thus, it is the lower part where the reduction of iron oxides ( and ) takes place.
The reactions taking place in the lower temperature range (500 – 800 K) in the blast furnace are:
The reaction taking place in the higher temperature range (900 – 1500 K) in the blast furnace are:
The silicate impurities of the ore is removed as slag by calcium oxide (CaO), which is formed by the decomposition of limestone .
4. Write chemical reactions taking place in the extraction of zinc from zinc blende.
Ans. The different steps involved in the extraction of zinc from zinc blende (ZnS) are given below:
(i) Concentration of ore
First, the gangue from zinc blende is removed by the froth floatation method.
(ii) Conversion to oxide (Roasting)
Sulphide ore is converted into oxide by the process of roasting. In this process, ZnS is heated in a regular supply of air in a furnace at a temperature, which is below the melting point of Zn.
(iii) Extraction of zinc from zinc oxide (Reduction)
Zinc is extracted from zinc oxide by the process of reduction. The reduction of zinc oxide is carried out by mixing it with powdered coke and then, heating it at 673 K.
(iv) Electrolytic Refining
Zinc can be refined by the process of electrolytic refining. In this process, impure zinc is made the anode while a pure copper strip is made the cathode. The electrolyte used is an acidified solution of zinc sulphate (ZnSO4). Electrolysis results in the transfer of zinc in pure from the anode to the cathode.
Anode:
Cathode:
5. How can you separate alumina from silica in bauxite ore associated with silica? Give equations, if any.
Ans. To separate alumina from silica in bauxite ore associated with silica, first the powdered ore is digested with a concentrated NaOH solution at 473 – 523 K and 35 – 36 bar pressure. This results in the leaching out of alumina as sodium aluminate and silica as sodium silicate leaving the impurities behind.
Then, gas is passed through the resulting solution to neutralize the aluminate in the solution, which results in the precipitation of hydrated alumina. To induce precipitation, the solution is seeded with freshly prepared samples of hydrated alumina.
During this process, sodium silicate remains in the solution. The obtained hydrated alumina is filtered, dried, and heated to get back pure alumina.
6. Giving examples, differentiate between ‘roasting’ and ‘calcination’.
Ans. Roasting is the process of converting sulphide ores to oxides by heating the ores in a regular supply of air at a temperature below the melting point of the metal. For example, sulphide ores of Zn, Pb, and Cu are converted to their respective oxides by this process.
On the other hand, calcination is the process of converting hydroxide and carbonate ores to oxides by heating the ores either in the absence or in a limited supply of air at a temperature below the melting point of the metal. This process causes the escaping of volatile matter leaving behind the metal oxide. For example, hydroxide of Fe, carbonates of Zn, Ca, Mg are converted to their respective oxides by this process.
7. The choice of a reducing agent in a particular case depends on thermodynamic factor. How far do you agree with this statement? Support your opinion with two examples.
Ans.
The above figure is a plot of Gibbs energy vs. T for formation of some oxides. It can be observed from the above graph that a metal can reduce the oxide of other metals, if the standard free energy of formationof the oxide of the former is more negative than the latter. For example, since is more negative than , Al can reduce to Cu, but Cu cannot reduce . Similarly, Mg can reduce ZnO to Zn, but Zn cannot reduce MgO because is more negative than .
8. Name the processes from which chlorine is obtained as a by-product. What will happen if an aqueous solution of NaCl is subjected to electrolysis?
Ans. In the electrolysis of molten NaCl, is obtained at the anode as a by product.
At cathode:
At anode:
The overall reaction is as follows:
If an aqueous solution of NaCl is electrolyzed, will be obtained at the anode but at the cathode, will be obtained (instead of Na). This is because the standard reduction potential of Na is more negative than that of (). Hence, will get preference to get reduced at the cathode and as a result, is evolved.
At cathode:
At anode:
9. What is the role of graphite rod in the electrometallurgy of aluminium?
Ans. In the electrometallurgy of aluminium, a fused mixture of purified alumina , cryolite and fluorspar is electrolysed. In this electrolysis, graphite is used as the anode and graphite-lined iron is used as the cathode. During the electrolysis, Al is liberated at the cathode, while CO and are liberated at the anode, according to the following equation.
Cathode:
Anode:
If a metal is used instead of graphite as the anode, then will be liberated. This will not only oxidise the metal of the electrode, but also convert some of the Al liberated at the cathode back into . Hence, graphite is used for preventing the formation of at the anode. Moreover, graphite is cheaper than other metals.
10. Outline the principles of refining of metals by the following methods:
(i) Zone refining
(ii) Electrolytic refining
(iii) Vapour phase refining
Ans. (i) Zone refining: This method is based on the principle that impurities are more soluble in the molten state of metal (the melt) than in the solid state. In the process of zone refining, a circular mobile heater is fixed at one end of a rod of impure metal. As the heater moves, the molten zone of the rod also moves along with it. As a result, pure metal crystallizes out of the melt and the impurities pass to the adjacent molten zone. This process is repeated several times, which leads to the segregation of impurities at one end of the rod. Then, the end with the impurities is cut off. Silicon, boron, gallium, indium etc. can be purified by this process.
(ii) Electrolytic refining: Electrolytic refining is the process of refining impure metals by using electricity. In this process, impure metal is made the anode and a strip of pure metal is made the cathode. A solution of a soluble salt of the same metal is taken as the electrolyte. When an electric current is passed, metal ions from the electrolyte are deposited at the cathode as pure metal and the impure metal from the anode dissolves into the electrolyte in the form of ions. The impurities present in the impure metal gets collected below the anode. This is known as anode mud.
Anode:
Cathode:
(iii) Vapour phase refining: Vapour phase refining is the process of refining metal by converting it into its volatile compound and then, decomposing it to obtain a pure metal. To carry out this process,
(i) the metal should form a volatile compound with an available reagent, and
(ii) the volatile compound should be easily decomposable so that the metal can be easily recovered.
Nickel, zirconium, and titanium are refined using this method.
NCERT Solution of Chemistry Chapter 6 Isolation of Elements
INTEXT Questions
Question 1. ( Isolation of Elements )
Which of the ores mentioned in Table 6.1 (NCERT Textbook) can be concentrated by magnetic separation method?
Solution:
Ores in which one of the components (either the impurity or the actual ore) is magnetic can be concentrated by magnetic separation, e.g., ores containing iron (haematite, magnetite, siderite and iron pyrites).
Question 2. ( Isolation of Elements )
What is the significance of leaching in the extraction of aluminium?
Solution:
Leaching is significant as it helps in removing the impurities like SiO2, Fe2O3, etc. from the bauxite ore.
Question 3. ( Isolation of Elements )
The reaction, Cr2O3 + 2Al → Al2O3 + 2cr (∆G° = – 421 kJ) is thermodynamically feasible as is apparent from the Gibbs energy value. Why does it not take place at room temperature?
Solution:
Certain amount of activation energy is essential even for such reactions which are thermodynamically feasible, therefore heating is required.
Question 4. ( Isolation of Elements )
Is it true that under certain conditions. Mg can reduce Al2O3 and Al can reduce MgO? What are those conditions?
Solution:
Yes, below 1350°C, Mg can reduce Al2O3 and above 1350°C, Al can reduce MgO. This can be inferred from ∆G° vs T plots.
NCERT Exercises
Question 1. ( Isolation of Elements )
Copper can be extracted by hydrometallurgy but not zinc. Explain.
Solution:
The E° of zinc (Zn2+/Zn = – 0.76 V) is lower luau that of copper (Cu2+/Cu = +0.34 V). Hence, zinc can displace Cu from solutions of Cu2+ ions.
But all these metals react with water forming their corresponding ions with the evolution of H2 gas. Hence, Al, Mg, etc. cannot be used to displace zinc from the solution of Zn2+ ions. Thus, copper can be extracted by hydrometal-lurgy but not zinc.
Question 2. ( Isolation of Elements )
What is the role of depressant in froth-floatation process?
Solution:
In froth -floatation process, the role of the depressant is to prevent one type of sulphide ore particles from forming the froth with air bubbles. For example, NaCN is used as a depressant to separate lead sulphide (PbS) ore from zinc sulphide (ZnS) ore. The reason is that NaCN forms a zinc complex, Na2[Zn(CN)4] on the surface of ZnS preventing it from the formation of the froth. Under these conditions, only PbS forms froth and therefore, it can be separated from ZnS ore.
Question 3. ( Isolation of Elements )
Why is the extraction of copper from pyrites more difficult than that from its oxide ore through reduction?
Solution:
In the Ellingham diagram, the Cu2O line is almost at the top. So it is quite easy to reduce oxide ores of copper directly to the metal by heating with coke (as can be seen in graph that the lines of C, CO and C, CO2 are at much lower positions). But most of the ores are sulphide and some may also contain iron. So, the sulphide ores are roasted/smelted to give oxides :
Question 4. ( Isolation of Elements )
Explain : (i) Zone refining (ii) Column chroma-tography.
Solution:
(i) This method is based on the principle that the impurities are more soluble in the melt than in the solid state of the metal. A circular mobile heater is fixed at one end of a rod of the impure metal. The molten zone moves along with the heater which is moved forward. As the heater moves forward, the pure metal crystallises out of the melt and the impurities pass on into the adjacent molten zone. The process is repeated several times and the heater is moved in the same direction. At one end, impurities get concentrated. This end is cut off. This method is very useful for producing semiconductor and other metals of very high purity, c.g., germanium, silicon, boron, gallium and indium.
(ii) Chromatographic method is based on the principle that different components of a mixture are differently adsorbed on an adsorbent. The adsorbed components are removed (eluted) by using suitable (eluant). There are several chromatogrpahic techniques such as paper chromatography, column chromatography, gas chromatography etc.
Column chromatography : Column chroma-tography involves separation of a mixture over a column of adsorbent (stationary phase) packed in a glass tube. The column is fitted with a stopcock at its lower end (fig). The mixture adsorbed on adsorbent is placed on the top of the adsorbent column packed in a glass tube.
An appropriate eluant which is a liquid or a mixture of liquids is allowed to flow the column slowly. Depending upon the degree to which the compounds are adsored, complete separation takes place. The most readily adsorbed substances are retained near the top and others come down to various distance in the column.
Question 5. ( Isolation of Elements )
Out of C and CO, which is a better reducing agent at 673 K?
Solution:
When carbon acts as a reducing agent, it is either converted into CO or CO2 or both.
2C + O2 → 2CO
C + O2 → CO2
CO is oxidised to CO2 when it is used as a reducing agent.
2CO + O2 → 2CO2
From the Ellingham diagram (refer answer number 3), it is clear that at the temperature 673 K, the AG° of the formation of CO2 from CO is more negative than the formation of CO or CO2 from carbon. Hence, at temperature 673 K, CO is a better reducing agent than C.
Question 6. ( Isolation of Elements )
Name the common elements present in the anode mud in electrolytic refining of copper. Why are they so present?
Solution:
Many of the metals such as copper, silver, gold, aluminium, lead, etc., are purified by this method. This is perhaps the most important method. The impure metal is made anode while a thin sheet of pure metal acts as a cathode. The electrolytic solution consists of generally an aqueous solution of a salt or a complex of the metal. On passing the current, the pure metal is deposited on the cathode and equivalent amount of the metal gets dissolved from the anode. Thus, the metal is transferred from anode to cathode through solution. The soluble impurities pass into the solution while the insoluble one, especially less electropositive impurities collect below the anode as anodic mud or anode sludge. Impurities from the blister copper deposit as anode mud which contains antimony, selenium, tellurium, silver, gold and platinum.
Question 7. ( Isolation of Elements )
Write down the reactions taking place in different zones in the blast furnace during the extraction of iron.
Solution:
Near the bottom of the furnace (zone of combustion, 2170 K), coke first combines with air to form CO2 which then combines with more coke (zone of heat absorption, 1423 K) to form CO. The CO thus produced acts as the reducing agent and reduces iron oxide to spongy iron near the top of the furnace (zone of reduction, 823 K).
At the lower part of the furnace (zone of fusion, 1423-1673 K) the spongy iron melts and dissolves some carbon, S, P, SiO2, Mn, etc.
The molten slag being less dense floats over the surface of the molten iron. The molten iron is then tapped off from the furnace and is then solidified to give blocks of iron called cast iron or pig iron.
Question 8. ( Isolation of Elements )
Write chemical reactions taking place in the extraction of zinc from zinc blende.
Solution:
Concentration : When zinc blende is used, the powdered ore is concentrated by froth-floatation process.
Roasting : The concentrated ore is heated in excess of oxygen at about 900°C. Zinc sulphide is oxidised to zinc oxide. If some of the ore is oxidised to zinc sulphate, it also decomposes at 900°C into ZnO.
For roasting, a reverberatory furnace may be used.
Reduction : The principal reaction that takes place during reduction is the conversion of the oxide into the metal with the help of carbon.
Electrolytic refining : Purification of zinc is done by electrolytic refining using pure Zn as cathode and impure Zn as anode. The electrolyte is ZnSO4.
Reaction at cathode : Zn2+(aq)+ 2e– → Zn(s)
Reaction at anode : 2H2O(l) → O2(g)+ 4H+(aq)+ 4e–
ZnSO4 electrolyte is added from time to time.
Question 9. ( Isolation of Elements )
State the role of silica in the metallurgy of copper.
Solution:
Iron present in pyrites has greater affinity for oxygen than copper. The copper oxide formed reacts with unchanged iron sulphide to form iron oxide so, most of the iron sulphide is oxidised to ferrous oxide.
2FeS + 3O2 → 2FeO + 2sO2
Ferrous oxide combines with silica which acts as flux and forms ferrous silicate. By this reaction most of the iron is removed as slag.
Question 10. ( Isolation of Elements )
What is meant by the term “chromatography”?
Solution:
Chromatographic method is based on the principle that different components of a mixture are differently adsorbed on an adsorbent. The adsorbed components are removed (eluted) by using suitable (eluant). There are several chromatogrpahic techniques such as paper chromatography, column chromatography, gas chromatography, etc.
Question 11. ( Isolation of Elements )
What criterion is followed for the selection of the stationary phase in chromatography?
Solution:
The stationary phase is selected in such a way that the impurities are more strongly adsorbed or are more soluble in the stationary phase than element to be purified. Under these conditions, when the column is extracted, the impurities will be retained by the stationary phase whereas the pure component is easily removed.
Question 12. ( Isolation of Elements )
Describe a method for refining nickel.
Solution:
Nickel is purified by Mond’s process. Impure nickel is treated with carbon monoxide at 60-80°C when volatile compound nickel carbonyl is formed. Nickel carbonyl decomposes at 180°C to form pure nickel and carbon monoxide.
Question 13. ( Isolation of Elements )
How can you separate alumina from silica in a bauxite ore associated with silica? Give equations, if any.
Solution:
Serpeck’s process is used when silica is present in considerable amounts in bauxite ore. The ore is mixed with coke and heated at 1800°C in presence of nitrogen, where AIN is formed.
Al2O3 + 3C + N2 → 2AlN + 3CO
Silica is reduced to silicon which volatilises off at this temperature.
SiO2 + 2C → Si + 2CO
Question 14. ( Isolation of Elements )
Giving examples, differentiate between ‘roasting’ and ‘calcination’.
Solution:
Calcination : It is the process of converting an ore into its oxide by heating it strongly below its melting point either in absence or limited supply of air.
Roasting : In roasting, the ore is heated in a regular supply of air in a furnace at a temperature below the melting point of the metal.
2 ZnS + 3O2 → 2ZnO + 2SO2
2 PbS + 3O2 → 2PbO + 2SO2
Question 15. ( Isolation of Elements )
How is’cast iron’different from ‘pig iron’?
Solution:
The iron obtained from Blast furnace contains about 4% carbon and many impurities in smaller amount (e.g., S, P, Si, Mn). This is known as pig iron and cast into variety of shapes.
Cast iron is different from pig iron and is made by melting pig iron with scrap iron and coke using hot air blast. It has slightly lower carbon content (about 3%) and is extremely hard and brittle.
Question 16. ( Isolation of Elements )
Differentiate between “minerals”and “ores’.
Solution:
The natural substances in which the metal or their compounds occur in the earth are called minerals. The mineral has a definite composition. It may be a single compound or complex mixture. The minerals from which the metals can be conveniently and economically extracted are known as ores. All the ores arc minerals but all minerals cannot be ores, e.g., both bauxite (Al2O3.xH2O) and clay (Al2O3.2SiO2.2H2O) are minerals of aluminium. It is bauxite which is used for extraction of aluminium and not clay. Thus bauxite is an ore of aluminium.
Question 17. ( Isolation of Elements )
Why copper matte is put in silica lined converter ?
Solution:
Copper matte consists of Cu2S and FeS. Wheia a blast of hot air is passed through molten matte taken in a silica lined converter, FeS present in matte is oxidised to FeO which combines with silica (SiO2) to form FeSiO3 (slag).
When complete iron has been removed as slag, some of the Cu2S undergoes oxidation to form Cu2O which then reacts with more Cu2S to form copper metal.
2CU2S + 3O2 → 2CU2O + 2SO2
2CU2O + Cu2S → 6Cu + SO2
Thus, copper matte is heated in silica lined converter to remove FeS present in matte as FeSiO3 (slag).
Question 18. ( Isolation of Elements )
What is the role of cryolite in the metallurgy of aluminium?
Solution:
The role of cryolite is as follows :
- It makes alumina a good conductor of electricity.
- It lowers the fusion temperature of the bath from 2323 K to about 1140 K.
Question 19. ( Isolation of Elements )
How is leaching carried out in case of low grade copper ores?
Solution:
The leaching of the low grade copper ores is carried out with acids in the presence of air when copper goes into solution as Cu2+ ions. Therefore,
Question 20. ( Isolation of Elements )
Why is zinc not extracted from zinc oxide through reduction using CO?
Solution:
The standard free energy of formation (∆fG°) of CO2 from CO is higher than that of the formation of ZnO from Zn. Hence, CO cannot be used to reduce ZnO to Zn.
Question 21. ( Isolation of Elements )
The value of ∆fG° for formation of Cr2O3 is – 540 kJ mol-1 and that of Al2O3 is – 827 kJ mol-1. Is the reduction of Cr2O3 possible with Al?
Solution:
Question 22. ( Isolation of Elements )
Out of C and CO, which is a better reducing agent for ZnO?
Solution:
The free energy of formation (∆f G°) of CO from C becomes lower at temperatures above 1120 K whereas that of CO2 from C becomes lower above 1323 K than ∆fG° of ZnO. However, ∆fG° of CO2 from CO is always higher than that of ZnO. Therefore, C can reduce ZnO to Zn but not CO. Therefore, out of C and CO, C is a better reducing agent than CO for ZnO.
Reduction of ZnO is usually carried out around
Question 23. ( Isolation of Elements )
The choice of a reducing agent in a particular case depends on thermodynamic factor. How far do you agree with this statement? Support your opinion with two examples.
Solution:
Some basic concepts of thermodynamics lielp us in understanding the theory of metallurgical transformations. Gibb’s energy is the most significant term.
The graphical representation of Gibb’s energy was first used by H.J.T. Ellingham. This
provides a sound basis for considering the k choice of reducing agent in the reduction of oxides. This is known as Ellingham diagram. (Tor diagram refer answer number 3) Such diagrams help us in predicting the feasibility of thermal reduction of an ore. The criterion of feasibility is that at a given temperature Gibb’s energy of the reaction must be negative.
Examples :
(i) Thermodynamics helps us to understand how coke reduces the oxide and why blast furnace is chosen. One of the main reduction steps in this process is :
FeO(s) + C(s) → Fe(s/l) + CO(g)… (1)
It can be seen as a couple of two simpler reactions. In one, the reduction of FeO is taking place and in the other, C is being oxidised to CO :
When both the reactions take place to yield the equation (1), the net Gibb’s energy change becomes :
Naturally, the resultant reaction will take place when the right hand side in equation (3) is negative. In ∆G° vs T plot representing reaction 2, the plot goes upward and that representing the change C → CO (C, CO) goes downward. At temperatures above 1073 K (approx), the C, CO line comes below the Fe, FeO line [∆G(c,co) < ∆G(Fe,FeO)] So in this range, coke will be reducing the FeO and will itself be oxidised to CO. In a similar way the reduction of Fe3O4 and Fe2O3 at relatively lower temperatures by CO can be explained on the basis of lower lying points of intersection of their curves with the CO, CO2 curve in Ellinghan diagram.
(ii) In the graph of ∆r.G° vs T for formation of oxides, the Cu2O line is almost at the top. So it is quite easy to reduce oxide ores of copper directly to the metal by heating with coke (both the lines of C, CO and C, CO2 are at much lower position in the graph particularly after 500 – 600 K). However most of the ores are sulphide and some may also contain iron. The sulphide ores are roasted/smelted to give oxides:
2CU2S + 3O2 → 2Cu2O + 2SO2
The oxide can then be easily reduced to metallic copper using coke.
Cu2O + C → 2Cu + CO
Question 24. ( Isolation of Elements )
Name the processes from which chlorine is obtained as a by-product. What will happen if an aqueous solution of NaCI is subjected to electrolysis?
Solution:
Sodium metal is prepared by Down’s process. This process involves the electrolysis of a fused mixture of NaCI and CaCl2 at 873 K. During electrolysis, sodium is discharged at the cathode and Cl2 is obtained at the anode as a by-product.
Question 25. ( Isolation of Elements )
What is the role of graphite rod in the electrometallurgy of aluminium?
Solution:
In this process, a fused mixture of alumina, cryolite and fluorspar (CaF2) is electrolysed using graphite as anode and steel as cathode. During electrolysis, Al is liberated at the cathode whereas CO and CO2 are liberated at the anode.
If some other metal is used as the anode other than graphite, then O2 liberated will not only oxidise the metal of the electrode but would also convert some of the Al liberated at the cathode back to Al2O3. Since graphite is much cheaper than any metal, graphite is used as the anode. So, the role of graphite in electrometallurgy of Al is to prevent the liberation of O2 at the anode which may otherwise oxidise some of the liberated Al back to Al2O3.
Question 26. ( Isolation of Elements )
Outline the principles of refining of metals by the following methods :
- Zone refining
- Electrolytic refining
- Vapour phase refining
Solution:
(i) Refer answer number 4(i).
(ii) In this method, the impure metal is made to act as anode. A strip of the same metal in pure form is used as cathode. They are put in a suitable electrolytic bath containing soluble salt of the same metal. The more basic metal remains in the solution and the less basic ones go to the anode mud.
Anode : M → Mn+ ne–
Cathode : Mn+ + ne– → M
Copper is refined using an electrolytic method. Anodes are of impure copper and pure copper strips are taken as cathode. The electrolyte is acidified solution of copper sulphate and the net result of electrolysis is the transfer of copper in pure form from the anode to the cathode :
Anode : Cu → Cu2+ + 2e–
Cathode : Cu2+ + 2e– → Cu
Impurities from the blister copper deposit as anode mud which contains antimony, selenium, tellurium, silver, gold and platinum; recovery of these elements may meet the cost of refining.
Zinc may also be refined this way.
(iii) In this method, the metal is converted into its volatile compound and collected elsewhere. It is then decomposed to give pure metal. So, the two requirements are :
(a) The metal should form a volatile compound with an available reagent.
(b) The volatile compound should be easily decomposable, so that the recovery is easy.
Following example will illustrate this technique.
Mond process for Refining Nickel : In this process, nickel is heated in a stream of carbon monoxide forming a volatile complex, nickel tetracarbonyl :
The carbonyl is subjected to higher temperature so that it is decomposed giving the pure metal :
Question 27. ( Isolation of Elements )
Predict conditions under which Al might be expected to reduce MgO.
Solution:
The two equations are :
Related Links
Class 9th
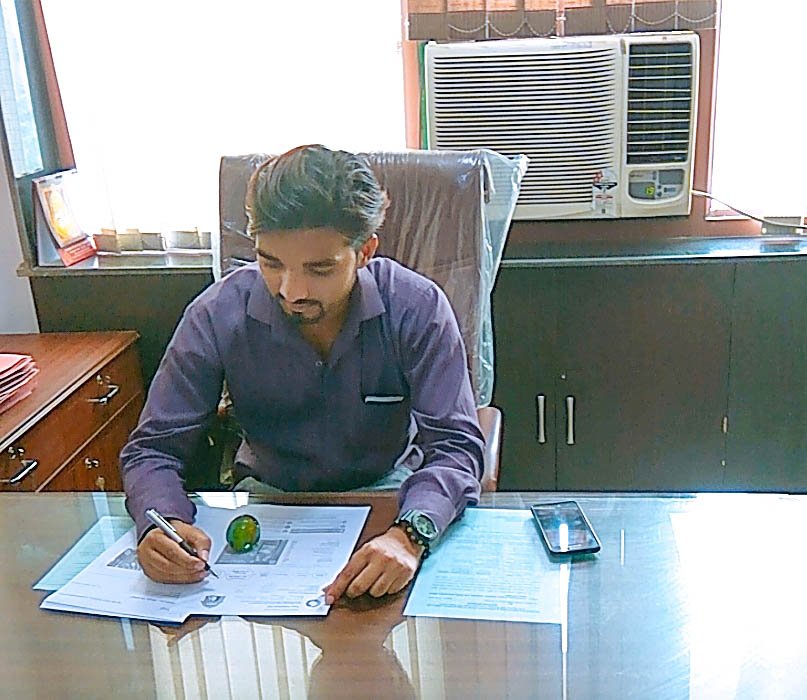
Mohd. Sharif Qualification: B.Tech (Mechanical Engineering) [Founder of Wisdom Academy] [Aim Foundation & Free-Education.In] [Engineer By Profession | Teacher By Choice] [Blogger, YouTube Creator]